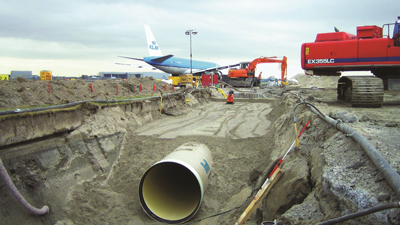
Sewage and Drainage System at Schiphol Airport in Amsterdam, NL
On June 21, 2012, Schipol Airport in Amsterdam has been chosen Europe’s Best Airport by ACI EUROPE (Airport Council International) for the third time. The Airport has been relying on the excellent characteristics of HOBAS Products since 2003 for HOBAS meets the high demands on product quality and short delivery times and therefore belongs to the few suppliers that are accepted to provide their goods and services. It is hardly surprising that Schiphol Airport prolonged the contracts for product deliveries another three years.
Schiphol has six runways and covers a total area of 2820 hectares, which is approximately 8 times the size of Central Park in New York. The paved airside spreads 1.2 million m2 asphalt and 3.8 million m2 concrete. Stormwater is conveyed in 30 km of culverts, 300 km of stormwater sewers and 125 km of concealed gutters – the complete drainage system totalling 455 km. Most of the reinforced concrete drainage underneath the airside’s paving has been installed in the 1960s.
Inspection of existing sewers
During the 1990s, Schiphol Airport checked the condition of its old sewers. Video inspections showed cracks in the concrete pipe material. More examinations followed detecting the severest damages in areas most heavily frequented by arriving and departing planes. The traffic load condition was therefore reevaluated with the conclusion that the Boeing 747 is mainly responsible for the damages on the reinforced concrete pipes.
Due to this situation and bearing in mind that the airport would have to be able to cope with larger aircraft such as the Airbus 380, which has a take-off weight of 590 tons, Schiphol opted for a renovation plan. The static calculations were based on a maximum weight of 750 tons in order to meet the requirements for the traffic loads of the latest generation of aircraft.
The plan involved renovating all concrete pipes beneath the paved airfield. Heavily damaged pipes beneath runways and taxiways were prioritized and involved a variety of diameters ranging from 300 to 1600 mm. Schiphol established a separate plan for each runway and taxiway for which the pipe sections running directly under the airstrips were kept as short as possible. Disruptions to air traffic had to be minimized so that Schiphol opted for trenchless installation methods such as relining and jacking.
3 Installation Methods
Pipes running directly beneath runways, taxiways and aprons have to withstand exceptional traffic loads. Their minimal nominal stiffness lies at 16000 N/m². For the project at Schipol Airport, three types of HOBAS CC-GRP Pipe Systems were employed:
HOBAS Relining Pipes were used for relining affected concrete culverts that cross the runways and taxiways and have a relatively small angular deflection. By inserting GRP Pipes in the existing structure, the line withstands the full traffic loads and obtains the complete lifetime and amortization period of a new sewer. A crawler crane inserted the GRP Pipes into the given structure from a starting pit. The annular space between the old and new pipe was subsequently filled with grout to uniformly distribute the loads on the sliplined pipes. Masonry connections link the GRP Pipes to concrete shafts.
HOBAS Jacking Pipes were utilized where the pipe diameter had to be maintained and where opening a trench was not an option. After completing the jacked line, the old pipe was filled with cellular concrete to prevent it from collapsing.
HOBAS SewerLine Pipes were installed beneath all paved areas where an open trench was feasible but also on the open field.
A total of 12.8 km HOBAS GRP Pipes have been installed at Schiphol Airport. All parties involved in the project are more than satisfied with the result – Schipol Airport is ready for the takeoff and landing of future giant aircrafts.
More information about this application
PROJECT DETAILS
Project ID: [13942] | |
Country: | Netherlands |
City: | Schipol |
Year: | 2003 |
Application: | Sewer |
Installation: | Microtunneling, Relining, Open Trench |
Technology: | Hobas |
Total Length: | 1280 m |
Nominal Diameter DN: | 300 | 1600 mm |
Nominal Pressure PN: | 1 bar |
Nominal Stiffness SN: | 16000 | 32000 N/m2 |